I’d never particularly wanted, or seen the need for a CNC machine, but the cheap, ubiquitous table top routers (“3018”, etc.) that have appeared on Amazon, Ebay and Youtube over the last few years sparked my interest – can you really get a working CNC machine for £150 ??
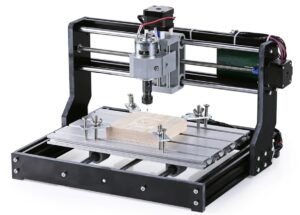
And so it begins…
After doing a bit of research on these types of machines (Youtube videos mainly!), I came to the conclusion that while they may function as described, they were pretty compromised when it came to machining. I briefly considered buying one to ‘upgrade’ but realised that pretty much everything about them would need to be replaced to do what I would want them to do.
My thoughts turned to building my own as an interesting project in its own right. I did a rough costing and it was clear that a homebuilt one would be much more expensive than Amazon, Ebay or Aliexpress offerings. The cost involved put me off the project – I didn’t want a CNC enough to spash out the best part of £1000 on nice, new bits, but the bug had bitten by then.
I then found out that a cheap Arduino could be used as a CNC controller and a bit of late night, alcohol assisted browsing of Aliexpress, Banggood and Amazon, and I had somehow ordered the cheapest spindle I could find, a pair of cheap Chinese linear rails, a ballscrew, a stepper motor and driver.
I should say that this project is a perfect example of how not to go about building a CNC – It’s something I drifted into and was not well defined. When I first started it, the intention was to be able to do some 3D relief carving in wood, but as it progressed, I realised that I really would like to machine aluminium, even if slowly.
The project grew legs and started running when an unused pair of 450mm long THK 15mm linear rails / bearings popped up on ebay and I managed to buy them for less than £40 (they would be over £400 new!)
Now I had to build something.
So, what do I want out of a machine?
I probably wasn’t honest with myself at this stage – what I told myself I wanted was:
- Maybe a bit of engraving
- Some 3D relief carvings in wood
- Produce prototype PCBs
- Possibly rout parts out of thin aluminium sheet
- Maybe, just maybe, machine parts out of aluminium, even if very slowly.
- ~0.1mm accuracy
- The ‘3018’ size of work area would be OK – roughly 300mm x 200mm
- Z travel of roughly 100mm to acommodate a work holding vice, drill bits, etc.
I know now that what I *really* wanted was something that would machine aluminium fairly competently.
A fixed gantry type machine seemed to be the easiest to build. I thought that with careful design, I could come up with a machine that was stiffer than many of the commonly seen arrangements, and so stand a better chance of machining metal.
I considered making the frame out of extruded aluminium sections, but mainly for perceived cost reasons I decided to fabricate a steel frame instead – I already had some bits of steel, and I could scrounge more. I told myself that a steel frame could be stiffer than aluminium, anyway.
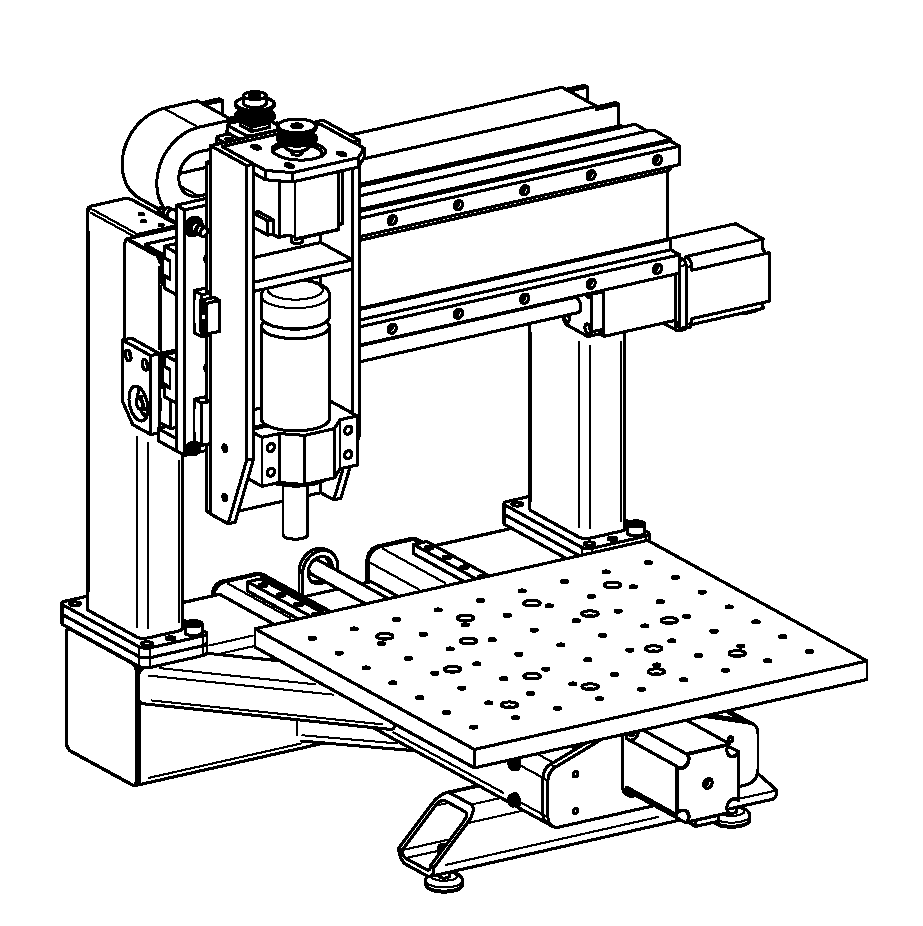
It may appear that there was a grand plan, but the truth is that the design evolved on the fly to suit whatever I could get hold of cheaply.