Bearings are a bit of an issue for these engines.
The ones in the previous post are bog-standard steel 608 bearings. Various people in the GTBA flung their hands up in horror at the prospect of ‘going back’ to using steel on steel bearings (even though the book gives them as an option) – they used to be OK in the good old days when you couldn’t get anything else, but inevitably failed (unless replaced regularly as a preventative measure), often taking the engine with them.
At the speeds involved, cages get torn apart by the centrifugal forces causing the bearing to collapse and whirly bits to hit non-whirly bits. There’s also a problem with steel balls in a steel race picking-up and seizing the bearing if the balls skate on the race for any reason (oil mist lubrication and preload springs help with the skating). The firm consensus was that steel bearings have been overtaken by full complement hybrid ceramic bearings.
The bearings are available from Boca in the US (list price $125 each!)
However the GTBA also provided a workaround…
If you can get hold of steel races and a supply of suitable silicon nitride balls, one can assemble one’s own bearings.
You can measure the balls in a steel bearing and order identically sized Si3N4 balls (Aliexpress, etc.) or, as I did, buy four (fairly cheap) caged hybrid bearings, dismantle them and re-arrange them into two full complement bearings.
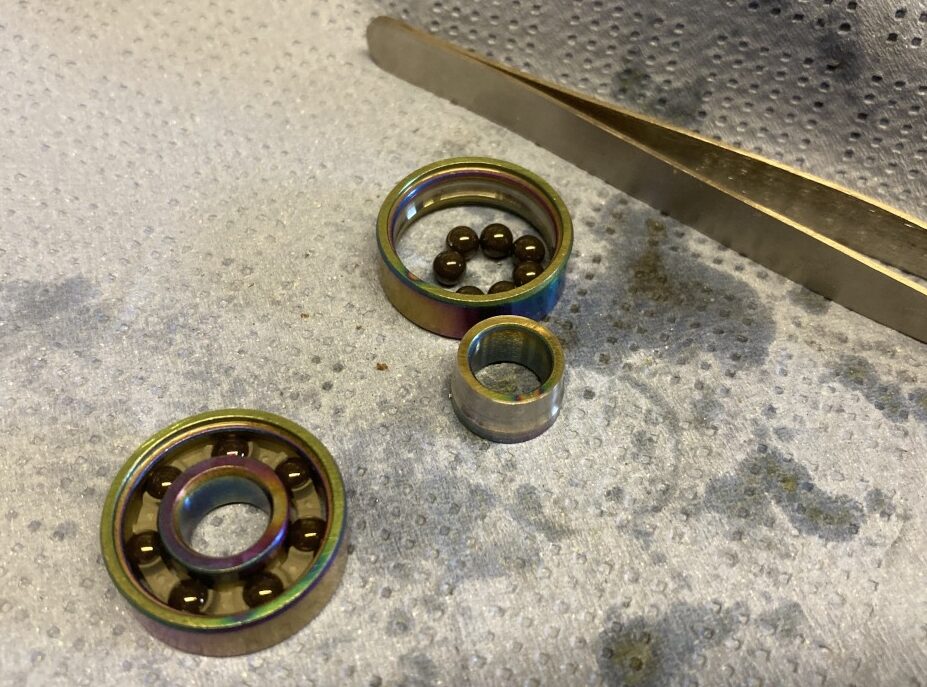
The key to getting it to work is to carefully machine down one side of the inner race at a slight taper without touching the bearing track itself.
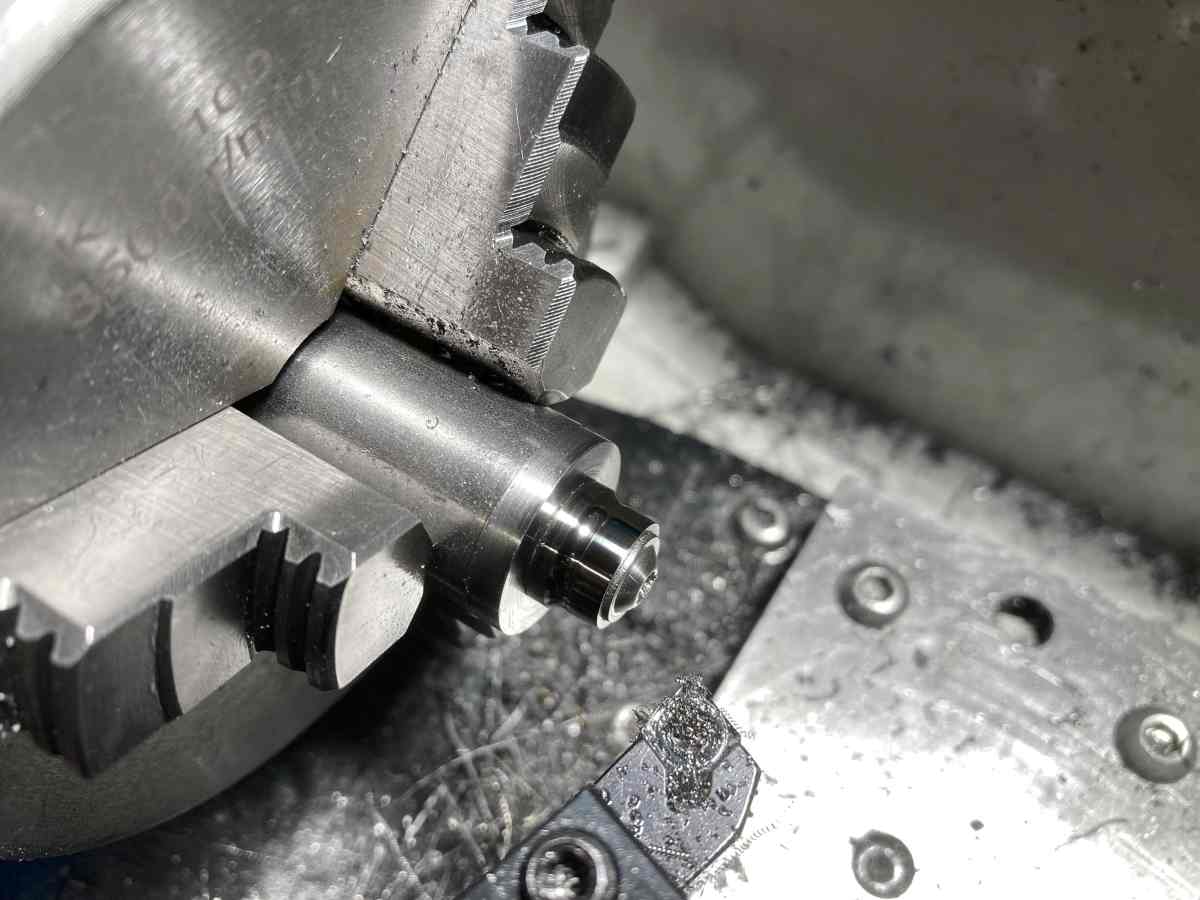
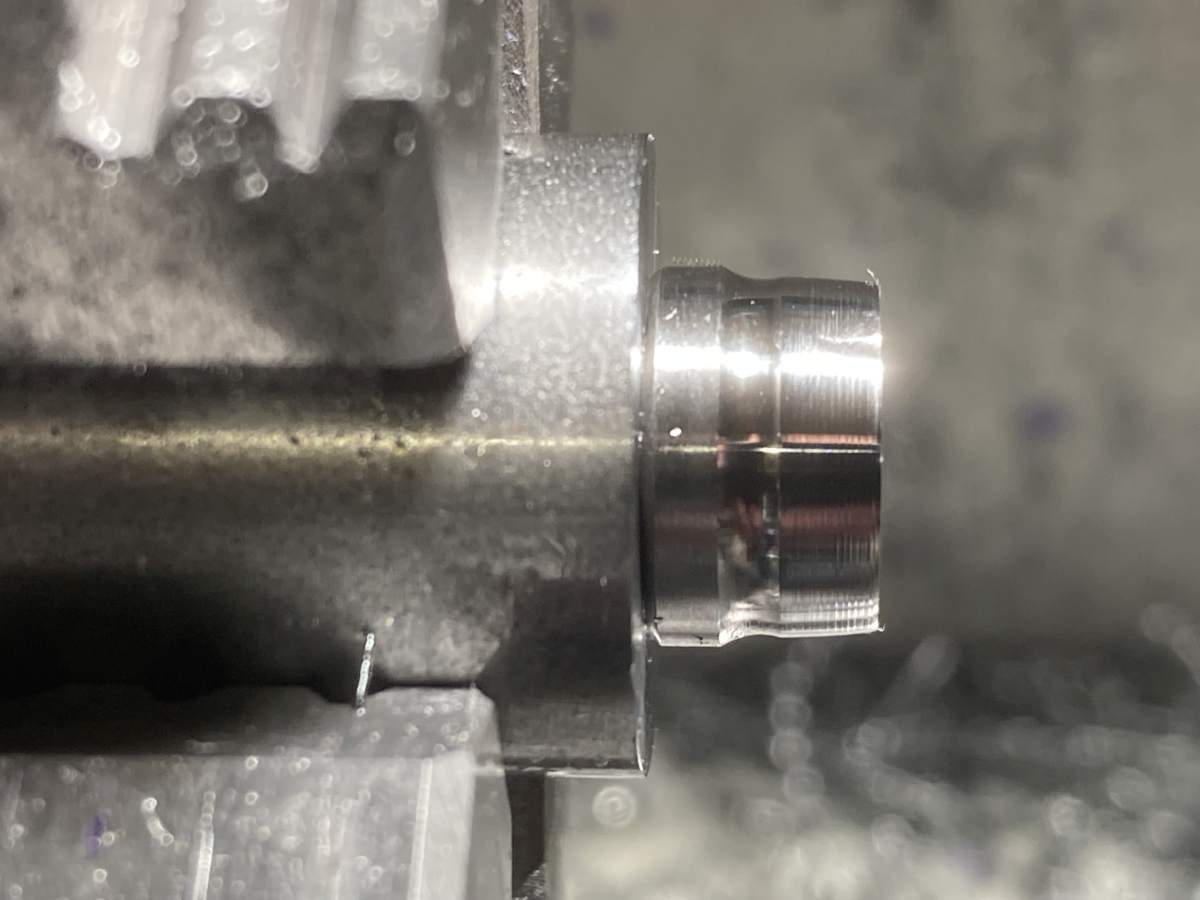
If you get it just right, the inner race will click into position inside a fully populated outer race:
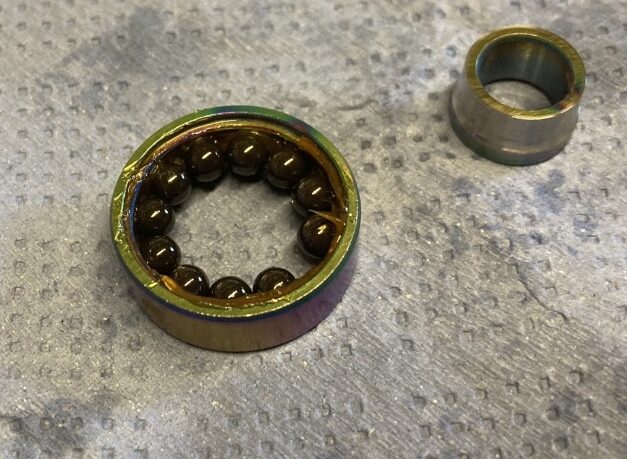
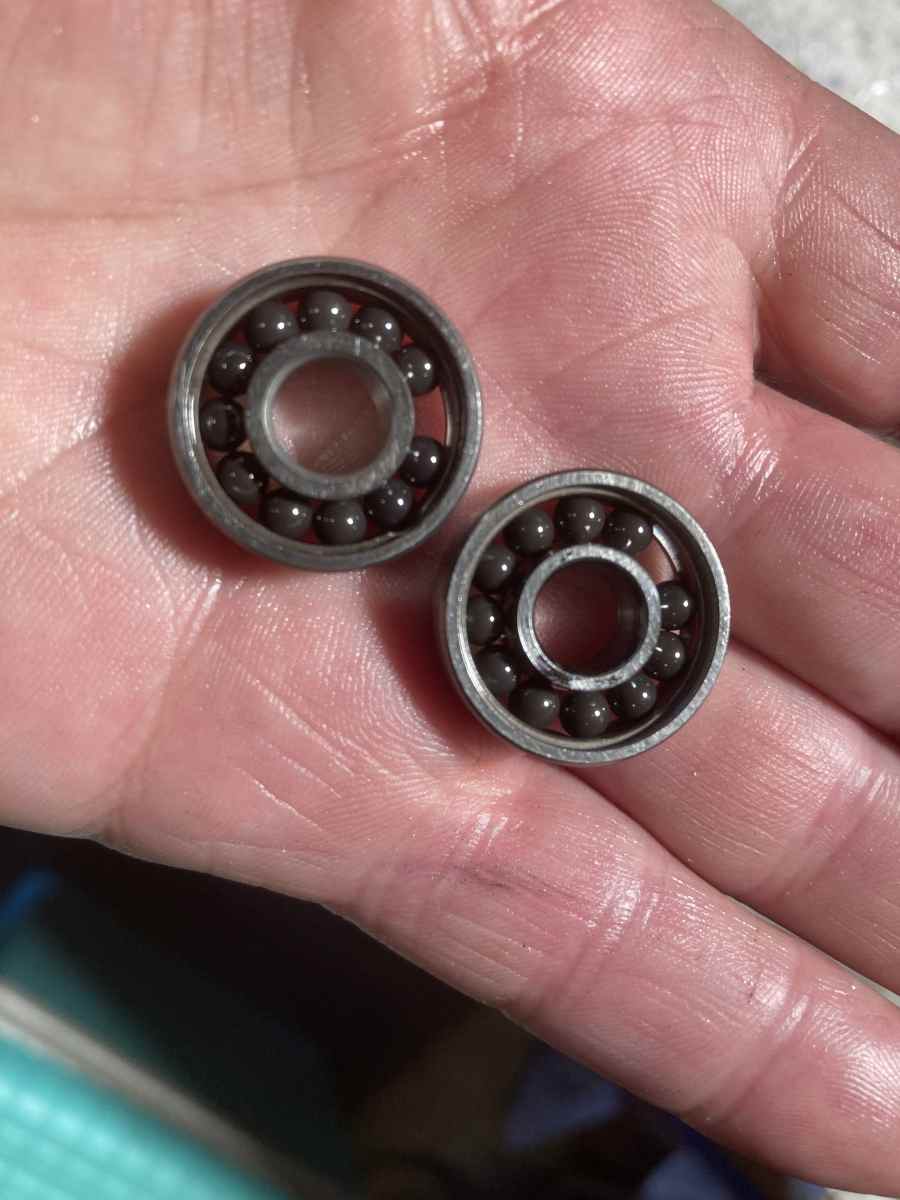
It sounds pretty straightforward as I write it here, but there was a heck of a lot more faffing than the description suggests!
Preload
Obviously bearings modified in this manner can’t support any load on the side of the race that has been machined away, so they need to be treated as angular contact bearings. They are assembled opposing each other and preloaded to ensure that the balls run on the ‘good’ face.
Preload is applied via a spring in front of the rear shaft bearing. I decided to use EPL 012 wave washers for this – they have quite a high spring rate (~30N/mm) so I have used two (separated by a spacer) to try and make the preload less sensitive to small changes in dimensions – 1.6mm installed height each should give me the 15N recommended in the book. The amount of preload can be adjusted by varying the thickness of the spacer.
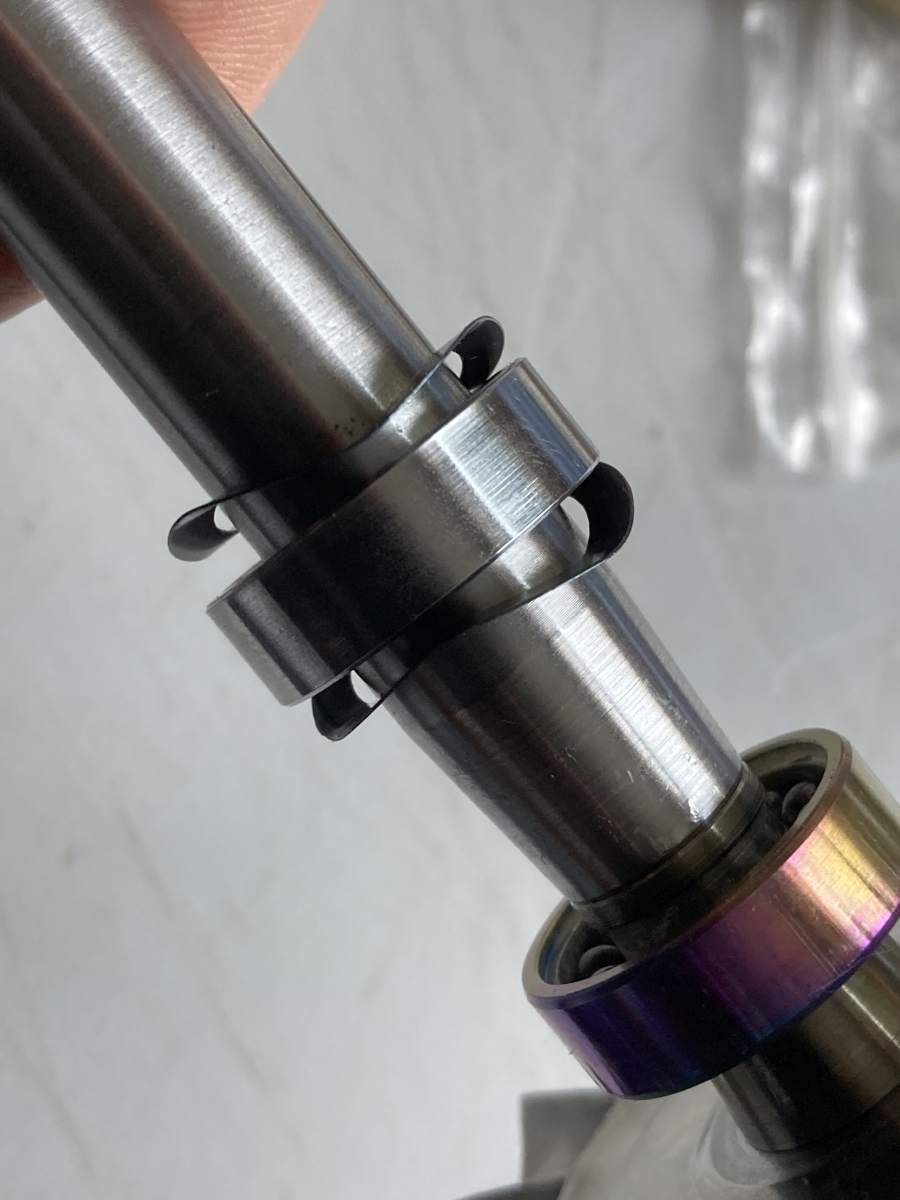
Lubrication
Current practice for this sort of engine seems to be to bleed air from the main casing into the shaft tunnel and use this to carry a kerosene / oil mist through the ball bearings to cool and lubricate them. The same mixture can be burned as the main fuel (like premixed 2 stroke fuel) and pressure can be taken from the main fuel supply so no separate oil tank or pump is needed (just a small bleed off the main fuel supply). The oil / kerosene coming through the shaft tunnel just gets burned up in the exhaust. I’m sure it isn’t good for fuel efficiency, but these are hideously inefficient anyway!